By Dave Robbins
More than six years after a catastrophic and fatal explosion on the MSC FLAMINIA container ship, the principal court cases on cause and liability in the New York District Court have come to an end. Burgoynes were instructed on the evening of the same day of the explosion, 14 July 2012, on behalf of the owners and ship management company and our personnel started the investigation the following day by travelling to interview evacuated crew.
The explosion occurred shortly after 08:00 hours, after white “smoke” had been reported escaping from one of the cargo holds of the 300 metre long container ship, around two hours earlier. Three crew sustained fatal injuries in the explosion and a further two were injured. At the time of the explosion, the vessel was in the middle of the Atlantic Ocean, having loaded containers in the Gulf ports of the USA and Mexico and was crossing to Europe.
The fire on the MSC FLAMINIA
In addition to the loss of the members of crew, the explosion caused extensive damage to the ship and its cargo to the extent that the substantial, steel bulkheads between holds were almost entirely destroyed. Hundreds of entire containers were consumed in the ensuing fire that burned for several days. Salvors attended the vessel and brought the fire under control before it spread to the accommodation and engine room.
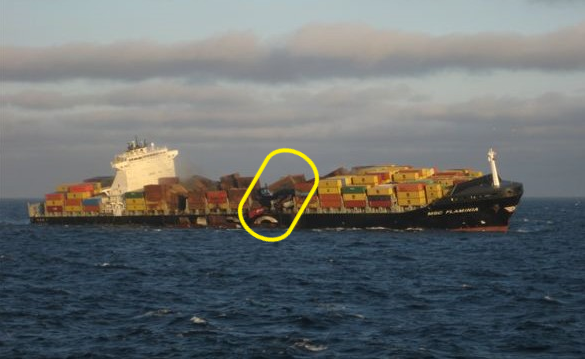
The MSC FLAMINIA listing after extinguishment of the fire which started as an explosion in the number four cargo hold indicated
Upon completion of the salvage operation, the vessel was returned to the Owners in Germany and inspections by the authorities were undertaken. After those inspections were finished, Burgoynes investigators commenced their investigation and inspections of the vessel. Key evidence was identified that had, because of the nature of the system it was collected from, survived the fire and its controlled removal was undertaken with Charterers’ representatives.
A series of investigative chemical analyses were then carried out on the retained items at a renowned surface chemistry laboratory in the UK. The analyses identified that the explosion was supported by a flammable vapour mixture in cargo hold 4 that originated from one of three 20’ ISO tanks of a hazardous chemical called Di-Vinyl Benzene (“DVB”). DVB is a monomer used in industry to make polymer plastics (as styrene is the monomer used to make polystyrene). DVB will self-react in a spontaneous, auto-polymerisation reaction and for that reason an inhibitor chemical is added to it at manufacture in order to stabilise it and to allow it to be transported. The inhibitor needs dissolved oxygen to be present in the DVB in order to work and it is used up slowly over time with the rate at which it is consumed increasing with increasing temperature.
If the inhibitor concentration falls, the auto-polymerisation reaction will commence, at first slowly. However, the reaction produces heat and if it is not brought under control, it will self-accelerate leading to significantly elevated temperatures, decomposition of the DVB and in the case of storage in ISO tanks, the escape of the decomposition products through the pressure relief valves on the tanks. In order to maximise the inhibitor life and the safe carriage time of the DVB, thermally insulated ISO tanks are used for carriage, which are loaded with the DVB cold.
The chemical analyses carried out on the retained exhibits indicated that the DVB had polymerised and decomposed, resulting in flammable decomposition products being expelled into the cargo hold at high temperature through the anticipated operation of pressure relief valves on the ISO tanks. It was those decomposition products that was the fuel for the explosion.
Showing the extent of damage to the cargo holds in the centre of the vessel
A review of reference sources and the circumstances surrounding the delivery of the three tanks of DVB to the vessel, indicated that the chemical had auto-polymerised, probably as a result of the fact it was loaded and stored at the port in Louisiana, in summer temperatures above 35 Celsius, with a mean temperature close to 30 Celsius. The tanks were left in an open yard exposed to the sun and the ambient temperatures for nearly ten days before loading on to the vessel. The manufacturer and the shipper were aware that DVB was temperature sensitive and standing company instructions were not to ship from southern US ports in summer months because of the high ambient temperatures and the risk to the stability of the DVB. The explosion occurred 14 days after loading the three ISO tanks of DVB on the ship.
Consequently, parties such as the manufacturer and the shipper of the DVB, became involved in the case and the investigative work focussed on the physical evidence on the ship. Owing to requests by such parties, a wide area of the ship, beyond the section where the DVB was stowed, was subject to controlled debris removal, which took place in Romania and later in Denmark. The investigation became a significant operation requiring co-ordination not only of our own technical investigation but also the requirements of other attending experts and those of the commercial contractors undertaking the debris removal work. Those requirements resulted in attendance on the vessel 24 hours a day, seven days a week from November 2013 to February 2014.
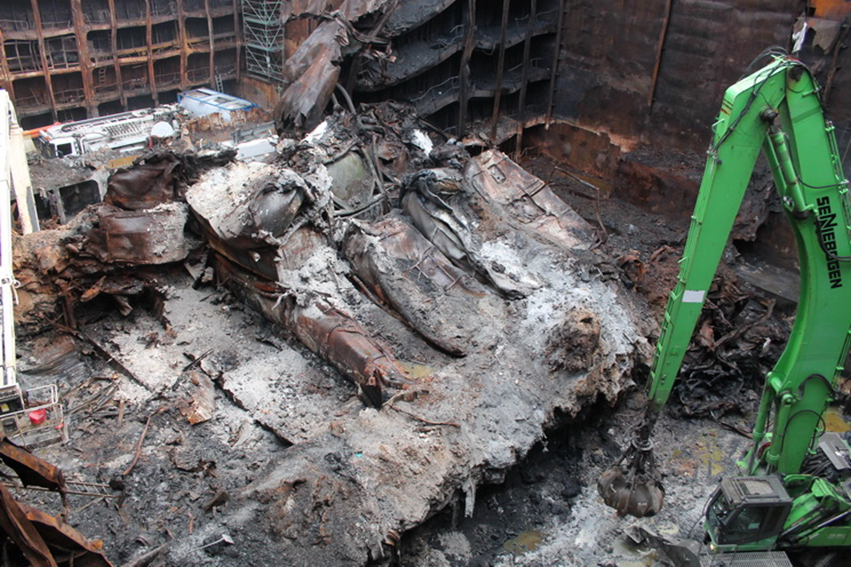
Showing a cargo hold during the clearance of debris and the remains of ISO tanks
Some further evidence was identified for analysis as a result of the inspections. Coordination with the other experts involved, who came from both sides of the Atlantic, resulted in agreement to joint testing at a single laboratory. Securing such an agreement was important in reducing the scope for later arguments being put forward that might otherwise have arisen if each of the parties had chosen to carry out individual testing at separate laboratories. The work, carried out in a laboratory in Denmark, was coordinated by Burgoyne chemists and metallurgists. In the event, the testing confirmed the early findings showing it was DVB that fuelled the explosion, though several of the parties still raised competing theories on the both the location and cause of the explosion.
Throughout the case, the Burgoynes’ scientists worked closely with both UK and US lawyers and in September 2017, a trial on causation took place in the New York District Court, in which Burgoynes' scientists gave evidence. The Court determined that the explosion was caused by the auto-polymerisation of DVB, with factors such as the temperature and time exposure history of the tanks being the key factors in leading to the DVB undergoing the reaction. In August 2018, the liability trial took place. The outcome of the trial was that the manufacturers and shippers of the DVB (joint Defendants) were together found 100% liable and that no liability attached to the other parties involved, including the Owners and their ship management company. The Defendants have lodged an appeal.
As a result of early investigations into the cause of the explosion that identified DVB as being the likely culprit for the explosion, by March 2015, the UN Secretariat on Dangerous Goods were suggesting four new UN codes (UN 3531, 3532, 3533 and 3534) for Polymerizing Substances that were assigned to Hazard Class 4.1 – self-reacting substances. The DVB had previously been assigned to Hazard Class 9 - Miscellaneous (Marine Pollutant), which led to the three ISO tanks of the chemical being stowed under deck. The classification of the chemical as Class 4.1 cargo requires that it be carried above deck where a confined flammable atmosphere cannot accumulate in the event that a self-accelerating polymerisation reaction occurs, which in turn would prevent a confined explosion. The International Group of P&I Clubs (IGP&I) has also issued guidance on the carriage of DVB in containers (https://www.igpandi.org/article/joint-industry-guidelines-carriage-dvb-containers).
Principal Burgoynes personnel involved: David Robbins (Lead Investigator), Richard Siddons (Chemical Engineer), Edward Hammersley (Chemist), Ian Wadsworth (Metallurgist and Materials Scientist), John Fuller (Chemical Engineer).