By Stuart Mortimore
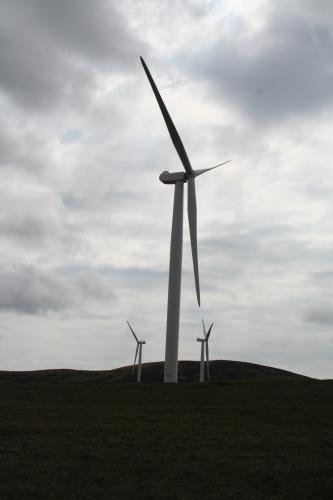
We will have all seen the graceful modern Quixotian structures that appear to spring up overnight, like mushrooms, by our roadsides. How many of us, however, have thought about what is inside these seemingly gentle giants? We all know that they convert wind energy into electricity but how many of us have thought, in detail, about how they work?
A modern wind turbine tower stands some fifty or more metres tall and it has to withstand, and where possible operate in, winds that range from breezes to gales. The structural engineering that is involved in withstanding gales and beyond is impressive enough. Add to this the mechanical engineering aspects of the design and the cleverness becomes more readily apparent.
Drive systems enable the heads (called nacelles) of large wind turbines to rotate into the wind and adjust the pitch of the blades of the machine so that useful energy can be extracted from winds with speeds that are anywhere between about three metres a second and twenty five metres a second. Such wind speeds cause the blades to rotate between approximately ten and twenty times a minute, with maximum power being extracted once the wind speed exceeds about ten metres a second. A gearbox connects the blades to the shaft of a generator, geared such that the shaft rotates at about one hundred times the speed of the blades, and there is also a brake system that can withstand the strongest winds and bring the whole drive train to a halt, if necessary, in a matter of seconds. Given a moment’s thought it soon becomes evident that we are looking at an engineering marvel.
Commercial wind turbines, as opposed to smaller models that are aimed toward the domestic market, come in a variety of sizes that ranges from a few hundreds of kilowatts to almost ten Megawatts, with these latter units generating sufficient electricity to power a small town. Most sets, however, are in the approximately two to three Megawatt range. Extracting such power without succumbing to the effects of fatigue is no mean feat.
Despite the foregoing, the cleverest part for me relates to the electrical equipment. This is because the machine has the ability to match varying wind speeds, and hence differing blade rotational speeds, to a national grid that runs at a constant “speed”, or frequency.
In a “conventional” power station, the generator will be driven at constant speed by a steam turbine, a gas turbine or some other form of prime mover, such as a diesel engine. The shaft of the generator that is connected to this prime mover, sometimes via a gearbox, will therefore also turn at constant speed. As a result, it is possible to use a type of machine that is known as a synchronous generator to generate electricity at a constant frequency, which in the UK is kept at 50 Hertz (or cycles per second).
In such a synchronous machine the shaft of the generator has an electromagnet (or electromagnets) built into it. As basic physics tells us, if a magnet is moved relative to a coil of wire, electricity will be generated within that coil. It follows, therefore, that if the electromagnet or electromagnets on the shaft are rotated at a constant speed the frequency of the electricity that is generated will also be constant. This is just what is needed in a national electricity distribution system.
In a wind turbine we do not have the luxury of a constant drive speed but we still need a constant electricity output frequency. The problem, therefore, is how to square this circle. This is where the genius comes in. The electrical designers have developed what might be described as a Machiavellian machine that appears to be different things to different systems. Specifically, part of it acts like a variable drive generator with the shaft rotating at a rate that is proportional to the blade rotational speed whereas the remainder of it acts like a constant speed machine by providing a 50 Hz electrical output that enables it to be connected directly to the national grid. So how is it done?
A control circuit is incorporated into the generator that provides power to the electromagnets on the shaft (known as the rotor) of the machine. By varying the quantity of power that is supplied to the groups of electromagnets at carefully selected frequencies, a magnetic field is produced that rotates at a different speed to that of the rotor. This has the effect of making the electromagnets rotate at a different speed to the shaft itself. As a result, the windings on the stationary part of the generator (which is known as the stator) see a magnet that rotates at a speed that equates to 50 Hz whereas rotor itself may be rotating considerably faster or slower than this speed. The stator, however, responds to what it “sees” and generates a 50 Hz output. Naturally, as wind speeds pick up and drop off continuously as the wind gusts and varies, the control process needs to keep one step ahead of these variations by continuously adjusting the electromagnetic rotational speeds.
Not surprisingly such complex machines can go wrong at times and with the total capacity in the UK projected to grow from about 2.4 GigaWatts in early 2010 to approximately 32 GigaWatts in 2020, at which time it is expected to constitute about 30% of total UK generation, wind generation is certainly a growth industry. Faults in such machines include fatigue related issues and other mechanical / materials failures, which can result in a variety of problems including gearbox failures, binding brakes, blade pitch control faults and even the rather dramatic shedding of blades. Electrical equipment can also go wrong, leading to control and stability problems and, in extreme cases, fires. Water cooling is employed in some electrical equipment and that can itself present a number of problems. Although comparatively rare, management and safety issues also arise leading to personal injury claims and prosecutions.
Our fee earners have, between them, experience in mechanical and electrical engineering, and materials science, as well as an enviable reputation in fire and explosion investigations. Moreover we have experience of working with electricity generation and distribution equipment of various types, including wind turbines, with some of this experience being gained whilst working for major power generation equipment companies. Burgoynes, with its wide geographic coverage both at home and abroad, is therefore well placed to assist with most types of fault and problem analysis, in addition to determining the cause of any fire or explosion that may occur.
Principal Contacts
Stuart Mortimore, Glasgow Office